What Are the Different Types of Container Sight Glass?
- likemetals
- Apr 14
- 5 min read
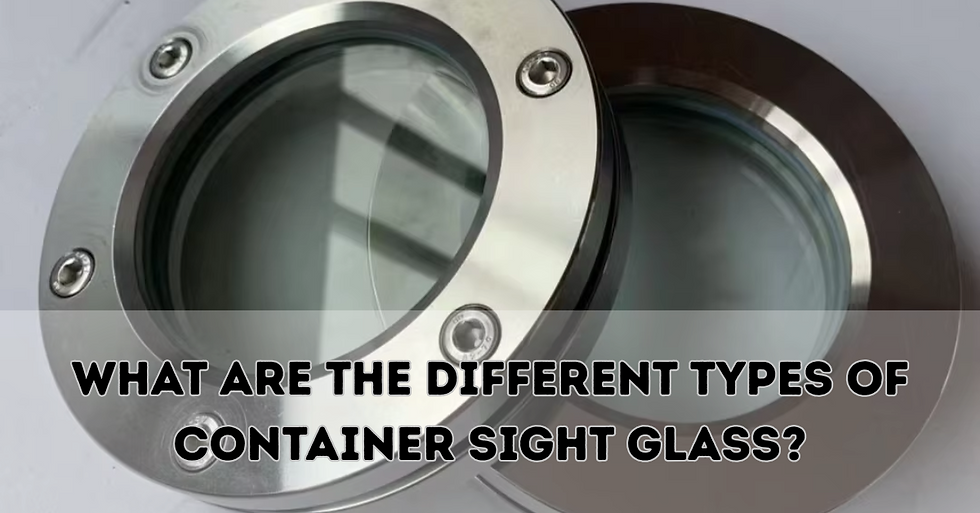
In today's industrial landscape, reliable process monitoring and visual inspection of liquid levels are crucial to ensuring safety and efficiency. One key tool that makes this possible is the container sight glass. A container sight glass provides a clear visual indication of the contents of a tank, vessel, or container, enabling rapid assessments without the need for complex instrumentation. In this article, we'll delve into the different types of container sight glass available in the market, explore their unique features and applications, and offer guidance on what to consider when selecting.
Understanding the Role of a Container Sight Glass
A container sight glass serves as the transparent window into the interior of industrial containers. Whether used in chemical processing, water treatment, food and beverage production, or pharmaceutical manufacturing, the sight glass offers real-time monitoring of liquid levels, detection of foam or sediment, and even confirmation of fluid clarity. This helps verify process continuity and enhances safety by allowing operators to spot potential issues before they escalate.
Key benefits of using a container sight glass include:
Immediate Visual Feedback: Operators can quickly verify the presence, level, and quality of liquids without interrupting the process.
Enhanced Safety: Quick monitoring helps detect leaks, blockages, or abnormal conditions, reducing risks.
Easy Maintenance: Many sight glasses are designed for easy removal and cleaning, ensuring longevity and unimpeded functionality.
Cost-Effectiveness: Sight glasses provide a robust yet economical means of process visualization by reducing the need for complex electronic sensors.
Types of Container Sight Glass
Different applications require different designs and features. The type of container sight glass you choose depends on factors such as the environment, the kind of liquid, the pressure conditions of the container, and maintenance considerations. Below are the main types of container sight glass:
1. Bolt-On (Bolt Mounted) Sight Glass
Description: Bolt-on sight glasses are mounted onto the vessel using bolts and gaskets. They typically consist of a frameless or framed glass window secured directly to the container's surface.
Features and Benefits:
Ease of Installation: The bolt-on design allows for relatively straightforward installation and removal for cleaning or maintenance.
Versatility: They can be applied to a variety of container shapes and sizes.
Reliability: Bolt-on sight glasses resist pressure and environmental conditions when adequately sealed with the correct gaskets.
Applications: Bolt-on models are often used in applications requiring regular maintenance or inspection, such as chemical processing plants and water treatment facilities.
2. Welded-In Sight Glass
Description: Welded-in sight glasses are permanently integrated into the container's structure through welding. This type is generally more robust due to the solid, permanent bond.
Features and Benefits:
Durability: The weld provides a secure, leak-proof integration, making these sight glasses ideal for high-pressure environments.
Low Maintenance: Being a permanent fixture, they require minimal maintenance besides occasional cleaning.
Aesthetic Integration: These designs often have a seamless appearance, which is preferred in applications where aesthetics matter.
Applications: Welded-in sight glasses are commonly found in high-pressure industrial tanks and environments where the sight glass will not need to be removed frequently for maintenance.
3. Clamp-On Sight Glass
Description: Clamp-on sight glasses attach externally to a container using clamps rather than bolts or welding. They are designed to be retrofitted onto existing vessels without significant modifications.
Features and Benefits:
Non-Invasive Installation: Suitable for retrofitting as they do not require permanent changes to the container.
Flexibility: Easily removed or repositioned if necessary.
Cost-Effective: Typically less expensive due to the more straightforward installation process.
Applications: Clamp-on sight glasses are popular in older facilities or where temporary installations are needed, such as in pilot plants or seasonal production lines.
4. Flanged Sight Glass
Description: Flanged sight glasses incorporate a flange that can be bolted or welded to the container. This design is used when a more rigid structural support is necessary.
Features and Benefits:
Enhanced Sealing: The flange design provides a solid, secure seal around the viewing area.
Structural Integrity: This type is more suited to high-stress environments requiring additional physical support.
Easy Integration: Flanged sight glasses integrate well with standard container designs with a flange plan.
Applications: These are typically used in environments with high pressures or heavy usage, such as petroleum refineries or high-capacity storage tanks.
5. Panel or Window Type Sight Glass
Description: Panel or window-type sight glasses are built into large viewing panels that may cover a significant section of the container wall. They provide a broad view of the internal conditions.
Features and Benefits:
Wide Viewing Area: This product offers extensive visibility, which is crucial for applications where the liquid level or quality needs to be monitored over a large area.
Customization: Often customizable to suit specific container dimensions or operational requirements.
Enhanced Monitoring: Ideal for processes that require continuous observation.
Applications: These types are used in large industrial tanks and process vessels where detailed visual monitoring is necessary.
Key Factors to Consider When Selecting a Container Sight Glass
When choosing a container sight glass, evaluating the following factors is essential:
Material Quality: The sight glass's material—typically tempered glass or high-grade acrylic—must withstand the chemical and thermal stresses of the process environment.
Pressure and Temperature Ratings: Ensure that the sight glass is rated appropriately for your container's operating pressures and temperatures.
Installation Method: Consider whether a bolt-on, welded, clamp-on, or flanged style best suits your existing container design.
Maintenance Requirements: Evaluate how often the sight glass needs to be removed for cleaning and maintenance, and choose a design that aligns with your operational needs.
Regulatory Compliance: Ensure the product complies with industry standards and regulations. This is particularly important in highly regulated industries like food, pharmaceuticals, and chemicals.
Customization Options: If your process requires custom dimensions or specifications, look for manufacturers who offer bespoke solutions.
Cost-Effectiveness: Balance the initial cost with long-term durability and ease of maintenance to ensure the best return on investment.
Applications of Container Sight Glass
Container sight glasses play a critical role in multiple industries:
Chemical Processing: Monitoring the level and quality of reactive liquids ensures safe and efficient chemical reactions.
Water Treatment Facilities: Operators can quickly verify fluid levels and the quality of the treated water.
Food and Beverage Production: Ensure hygiene and monitor processing stages without compromising product integrity.
Pharmaceutical Manufacturing: Precise visual monitoring supports quality control and regulatory compliance.
Oil and Gas: These sight glasses, which can withstand harsh environments, help monitor critical process variables in refineries and storage tanks.
Each application utilizes the unique properties of container sight glass to enhance operational safety, efficiency, and process control.
Conclusion
A container sight glass is invaluable to industrial process monitoring and safety. Each variety offers unique advantages tailored to different applications and operating environments, from bolt-on and welded designs to clamp-on, flanged, and panel types. Whether you need a high-pressure solution for a refinery, a customizable option for a chemical processing tank, or a retrofit-friendly clamp-on model, understanding the different types and their specific features is crucial.
By evaluating factors such as material quality, installation method, maintenance requirements, and compatibility with your operational conditions, you can select the ideal container sight glass to meet your needs. This investment enhances safety and efficiency and supports long-term reliability across various industrial applications.
For those looking to optimize process monitoring and reliability in your operations, partnering with an experienced supplier to source a high-quality container sight glass is the key to long-term success.
Comments